With Fassi, cranes embody efficiency in all working conditions
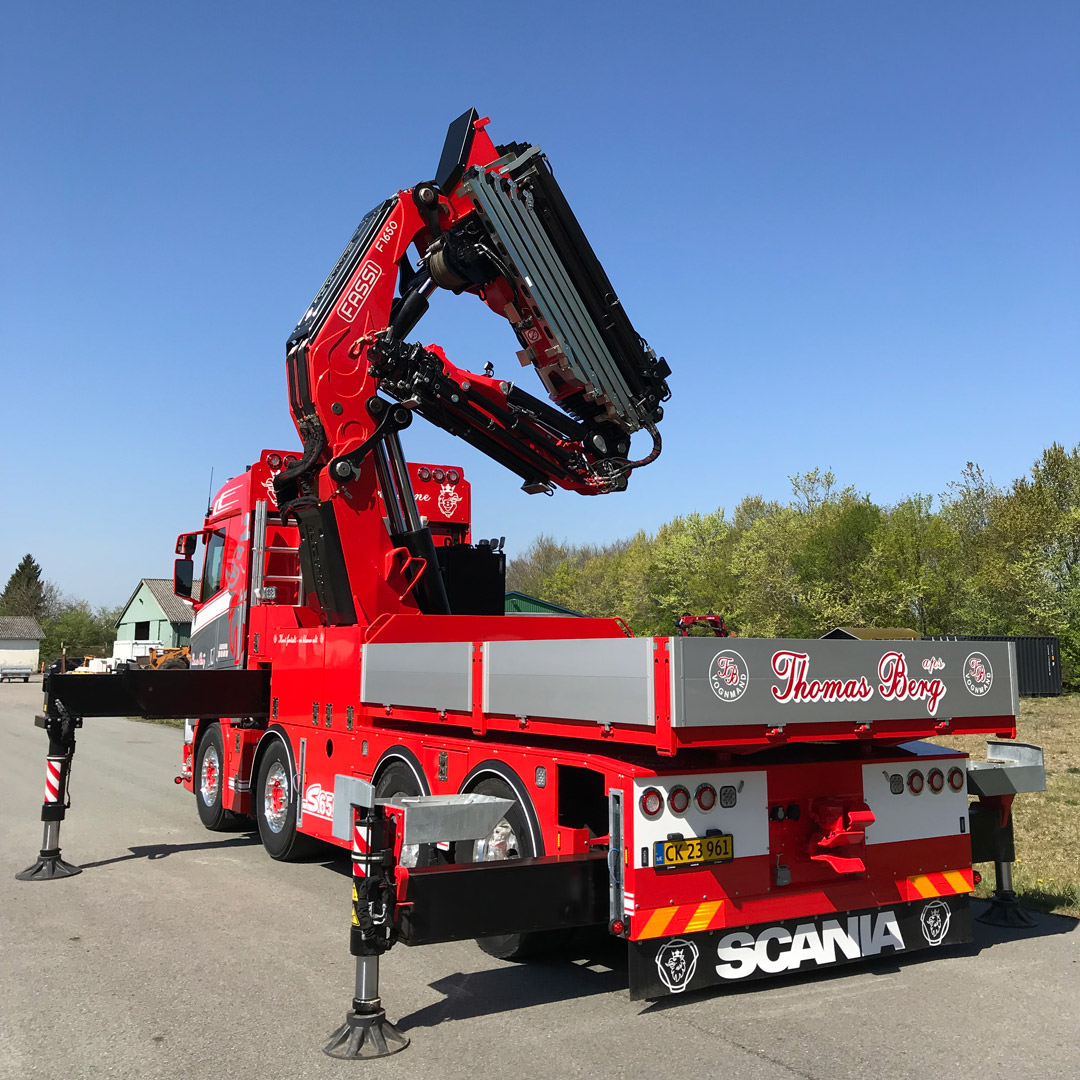
The best crane comes from a compromise between load capacity, stress cycles and weight. Performance on one side and efficiency on the other. That means, respectively, crane load capacity and the capacity to support intense and prolonged work cycles over time. Over 200,000 cycles, to be precise. These are features that are inextricably linked to each other and are at the foundation of the design and development of every Fassi crane, to guarantee high standards of efficiency.
The credit goes to the great care taken during the design and prototyping phase, the enormous amount of data derived from a long experience of manufacturing, the materials used, starting with the special steels, and to the tests carried out on the prototypes. In addition, there are the high levels of technology, electronics and automation, not forgetting the importance of maintenance, which is scheduled and constantly carried out.
The common thread that connects every step is always the same, the concept of efficiency. This means “constant performance capacity and compliance with its own functions and goals”.
The starting point is really the clear objectives that Fassi sets: development of a product able to face heavy work cycles while maintaining high-level performances and constant efficiency. To attain all that the following is needed: consolidated processes (that are at the same time flexible and open to innovation), expertise and skills, technology, timeliness, and knowledge of the market.
The possibility of exploiting the crane’s potential as much as possible becomes the fundamental target that forms the basis of every design phase, component production and product test.
In these interviews Rossano Ceresoli, R&D Manager of Fassi and Emilio Bertazzi, Fassi Sales Manager, explain respectively the processes that enable the development of high-performance and efficient cranes and the important implications for the market.
THE TECHNICAL POINT OF VIEW
Rossano Ceresoli, Fassi R&D Manager
What are the technical features of the crane that increase its longevity when performing heavy work cycles over a long period of time?
Cranes should have features that minimise the load concentration at the critical points: during the design phase, particular focus is given to the most stressed points. The control system also has to guarantee fluidity of movement that limits the stress peaks caused by accelerations and stops.
What design challenges do you face when developing cranes that can pass tests of 200,000 stress cycles?
Great care is given to the welded joints and their position on components, focusing on the geometric aspects of the welding and on the implementation procedures. For every variation in the parameters that compose the welding joint (such as steel quality, weld wire, joint geometry, temperature, execution speed, welding layers and last but not least the execution, which can be manual or automated), Fassi carries out several tests in order to identify the right execution in accordance with the requirements and the performances called for by the design.
How much do special steels contribute to the development of cranes that can support intense and prolonged work cycles?
The special steels – when properly employed – can have very good welding properties that increase the machine’s performances in terms of weight reduction and guaranteeing the crane’s strength and tenancy.
Which criteria are taken into account when defining a really efficient crane? The best crane comes from a compromise between load capacity and stress cycles. Is this always true?
The best crane comes from a compromise between load capacity, stress cycles and weight. On the top of that, you have to add ease of use and the possibility of exploiting the crane’s potential as much as possible: these aspects are managed by the electronic control system that allows optimal use of the crane in complete safety.
Has computer design contributed in a relevant way to the design of cranes that can face intense and prolonged work cycles?
Computer design allows us to speed up and verticalise the design phase. Nowadays the environment of pure design is integrated with that of engineering, so the designer can virtually design and simulate an idea and immediately check it with the analysis tools, such as FEM (Finite Element Method). However, considering all this as essential is a simplification; is a good investment enough to become a designer? No, it all has to be coupled with a deep knowledge of the product and of the materials, with a long experience of fatigue tests that we have been carrying out on all our projects since 1980 (that is, for 40 years) and with the vast experience accumulated after being on the market for 55 years. The computer is an excellent tool, but it has to be used by trained people with a lot of experience.
Which tests does Fassi use to check the crane’s capacity to take on prolonged work cycles? How close are they to reality?
In my opinion this is one of the most important strategic choices Fassi made at the beginning: to have in-house tools and people qualified to carry out the tests autonomously. Whether they are mechanic, metallurgic, environmental or procedural tests. Cranes have to be checked with structural calculations and experimental tests, from fatigue tests and measures that analyse the outreach, to confirming the calculations. The experimental tests are very accurate and allow us to simulate the real use of the crane in the field. In this way, we can guarantee that crane performances will be consistent over time.
Who certifies cranes designed in this way? And how?
According to current European regulations, the machine producer shall self-certify that its own product meets the safety requirements with respect to risk analysis and the observance of all mandatory legislations. The application of the EN 12999 regulation, which is the reference we use for our product, the CE declaration of conformity and its resulting certification mark represent a guarantee.
THE COMMERCIAL POINT OF VIEW
Emilio Bertazzi, Sales Manager of Fassi
Performance (in terms of load capacity) and efficiency (the capacity to support intense and prolonged work cycles over time) are two important requirements when choosing a crane. Which sectors prioritise one over the other?
Unfortunately, the two aspects are inextricably linked, no customer would accept a performance increase at the expense of efficiency and longevity and vice versa; therefore it’s not possible, in my opinion, to separate the two issues in our world and it is with this spirit that we design our cranes and put them on the market.
How sought-after is the service life of the crane in connection with prolonged performances? Why is such a feature so important?
Continuous and constant crane maintenance is the secret for a long product life. Over these 55 years of market experience, we have seen the benefits of systemic and scheduled maintenance in terms of average life of the crane. So, we can say without any doubts that maintenance becomes the most important element that allows the crane to be operational for a long time.
Do the customers know and ask for certificates pertaining to the crane’s capacity to face intense and prolonged work cycles over time?
Generally, they don’t. If the salesman doesn’t mention the issue of the work cycles, they are not normally taken into consideration by the customer during their evaluation of the product.
How much does the residual value of the crane factor into choice when a new crane is purchased?
When evaluating a used crane, the customer normally considers its aesthetic and functional appearance; it’s very difficult for him to evaluate the residual life of a crane. Firstly, because he doesn’t have the instruments to make an evaluation (normally there are no data on which he can base an evaluation) and secondly, the market normally evaluates the crane’s working hours without being able to calculate the average used load, which can help in understanding the crane’s average residual life in relation to the design parameters.
Lifting efficiency: crane efficiency coupled with maintenance scheduling. How is this concept applied on Fassi cranes?
Correct maintenance extends crane life, increases reliability, protects its value over time and last, but maybe most important, it makes it a safe machine. For this reason, we have developed in-house software which is integrated into the control systems and can interpret the crane work data and accordingly plan maintenance intervals to avoid any problems on the crane.
One of the strong points in the development of a Fassi crane is the welding process, a stage to which we dedicate time, materials and specialist personnel. This is because the welding has to be as perfect as possible in order to avoid any future failures caused by the stress levels of the materials or to the stresses they have to undergo. It also lowers the costs of maintenance over time. One of the objectives is to reduce the welding process to a minimum and once again Fassi has been able to attain high performance levels.